Becoming
World Class
Written By: Mario Cisneros
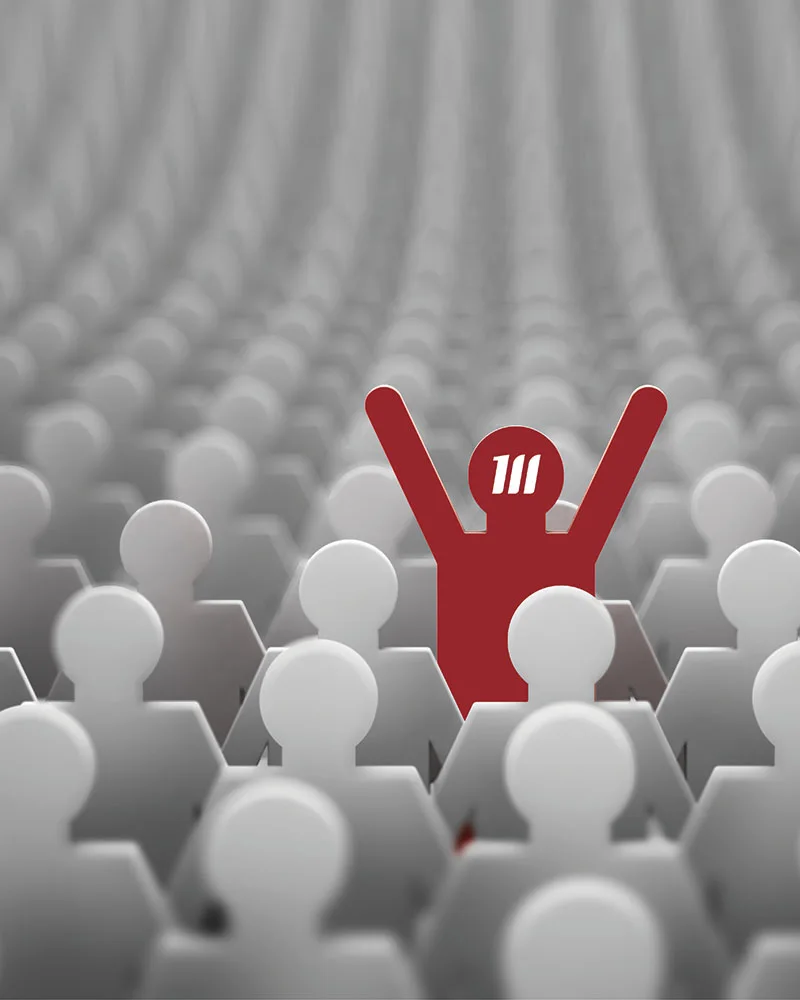
Having my vantage point every day as Med One’s National Director of Operations comes with the perspective of always wanting operations to achieve more. Resetting the bar in operations is the key to continuous improvements. Reaching for the next level of professional development is the next level of operational efficiency and excellence. Moving forward in operations is the only way we can become a world-class operation. We strive to reach that next level through continuous improvements. When I look at our offices, I see world-class potential in every location. I see facilities that could, in every circumstance, operate efficiently, seamlessly, with no scrambling to fill an order, no rescheduling of personnel, just the heartbeat of what a world-class operation should be.
Any business that has experienced rapid growth, much like us, must be looking to the horizon. For operations, that horizon tells us that continuous improvement must be part of our everyday scope. To become world-class in operations, Lean Six Sigma principles must be ingrained in our thought process. Professional development, efficiency, and operational excellence will only endure if Lean Six Sigma principles are used in every situation.
LEAN SIX SIGMA
Transportation
Inventory
Motion
Waiting
Over Production
Over Processing
Defects
Safety
Lean Six Sigma
The Lean Six Sigma methodologies of reducing waste were adopted by Toyota Manufacturing System, and it changed operations in every industry. It examines where you are, where you are going, and how to become world-class operationally. Awareness and self-examination are key factors. Managers have to look deep into what they are doing and the way they are doing it. This is the beginning of building the foundation of a fortress that will stand up to the whirlwinds that operations managers face daily. The easiest way to remember the eight wastes of LEAN Six Sigma is the acronym known as TIM WOODS.
The principles of Lean Six Sigma reduce waste in all aspects of operations, specifically the eight wastes of production. Anything and everything you do must be examined in its entirety to identify and remove the waste of that operation. That is the key -- by removing the waste, you are adding value.
Knowing the eight wastes associated with TIM WOODS and how to avoid them and/or reduce them in your facilities will dictate your success as an operational team. Many managers have by nature used certain principles of Lean Six Sigma without really knowing the actual principle of wasted reduction associated with them. But acquiring the full scope of Lean Six Sigma principles and the eight wastes associated with each category will safeguard all operations from some of the very tumultuous whirlwinds they face in their operational processes.
The Whirlwind Effect
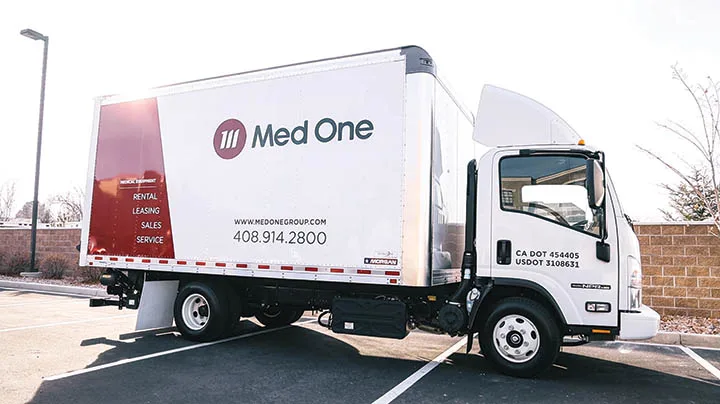
Operations managers face what is called the Whirlwind Effect the moment they arrive in their offices. The phone is ringing, vehicles have issues, there are equipment problems, personnel issues, billing issues, and deliveries that are urgent. With growth, the whirlwind effect seems to blow harder for an operations manager. They can easily be swept away by the ensuing gusts of the whirlwinds if they do not know where to find the right shelter from the daily storm. Some would say, “well, it’s just about training and knowing our customers’ needs.” I do not completely disagree that training and knowing customer needs are very important. However, operationally there must be a fortress to protect against the whirlwinds. This fortress must be built on the principles that will endure all the changing sizes and types of whirlwinds that may come. This fortress must be built on the solid, proven principles of Lean Six Sigma methodologies of reducing waste. If an operations manager allows the eight wastes to grow and endure at their facilities, their operations will be sent into a tailspin. This will lead to employee disappointment, disillusionment, and ultimately unsatisfied customers.
Building Your Fortress
Lean Six Sigma principles are documented principles. This will ensure every new person you hire and all current team members are being trained in all their tasks efficiently and effectively. When a team member knows their training is standardized and complete, it creates confidence in what they are doing and who they work for. This documentation becomes the method that is ingrained into the culture of a facility. Teams become more effective because they have been given the tools to be part of the solid fortress that has been built. This is how operations managers accomplish all of their goals today and see future growth.
Lean Six Sigma principles of reducing waste not only help in daily activities for employees, but they are important principles for managers to see the whole picture. Managers will experience many “Ah-ha” moments when examining a process in their facility and realize it falls into one of the categories of Lean Six Sigma waste.
“ Any business that has experienced
rapid growth,
much like us, must be looking to the horizon.
This experience is invaluable for a manager’s facility today and for management development in the future. Leading the training on a Lean Six Sigma process provides managers the tools needed to always repair their fortress if the whirlwinds of the day began to tear it down.
As a manager here at Med One, I know the most important hire for any facility is TIM WOODS. TIM WOODS teaches us how to reduce waste in operations. By reducing waste, we build in added value in operations. Knowing when one of the eight wastes occurs because the whirlwinds start to build up is when we as managers reach for that next level of operational excellence through the proven principles that will build the solid fortress. This is how we withstand the winds and build a legacy for the future.